

Traditional heating and its problems
Temperature is the most important parameter in ceramic synthesis. However, current heating technologies (e.g. box furnaces) are bulky and inefficient in energy use, requiring the entire furnace to heat the samples. Additionally, in this conventional heating approach, the temperature is often non-uniform in the heating zone. Furthermore, it is difficult to achieve high temperatures (up to 2000 K) and impossible to perform continuous manufacturing using a varied temperature profile.
​
-
Bulky
-
Slow
-
Uneven heating
-
CO2 emissions
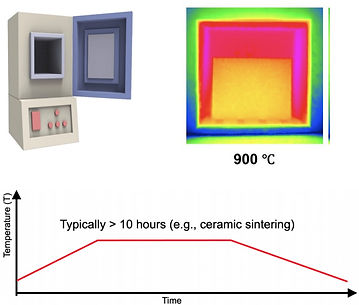
Limitations in synthesis
As a result, conventional ceramic and metal sintering often requires hours of furnace heating time. The long sintering time is particularly problematic for ionic materials (e.g., Li and Na conductors) for battery applications due to their severe volatility. The density of the sintered membranes is also low, which can increase the potential for short-circuiting of the cell. With conventional sintering, it is also impossible
to rapidly tune the sintering temperature profile to control the material’s microstructure toward desired properties. The poor temperature uniformity of the furnace also leads to low manufacturing yields and increases the cost of ceramic membranes.
​
-
Poor composition control (elementary loss)
-
Low density
-
Poor microstructure control
-
Low yield and high cost
-
CO2 generation

Severe lithium loss from lithium conductor during regular sintering for hours
High temperature synthesis but challenges
High temperature can exponentially increase the synthesis speed and overcome the challenges of elemental loss. Laser sintering, spark plasma sintering (SPS), flash sintering, and microwave sintering have all been developed with this aim. However, these high temperature processes have major challenges, particularly for membrane sintering and battery integration:
​
-
SPS is bulky and not compatible with roll-to-roll processing;
-
Flash sintering relies on current passing through the sample and is difficult to scale up;
-
Microwave sintering has challenges in achieving a uniform temperature (critical for membrane sintering).


Invention of Ultrafast High-temperature Sintering (UHS)

In response to these challenges and limitations, Professor Liangbing Hu invented a new sintering method for ceramics (Science, May 1, 2020, front cover). This technique, called ultrafast high-temperature sintering (UHS), can achieve temperatures of up to 3000 °C to thoroughly sinter metals and ceramics directly from their precursor powders toward dense final structures in seconds instead of hours. This process features multiple advantages, including:
-
Precise control of the sintering temperature;
-
Record high sintering temperatures in an open furnace design that allows continuous manufacturing;
-
Record high uniformity of the temperature profile.
UHS sintering addresses all the key sintering problems

Additionally, the UHS sintering method does not require pressure to be applied on the samples. As a result, we have been able to demonstrate continuous roll-to-roll UHS manufacturing.
-
Negligible loss (for Li , Na )
-
Super dense structure
-
Rapid sintering time from 10 hours to seconds
-
~ 100% yield (due to the uniform heating temperature)
-
All electrified by renewable energy
Continuous UHS Manufacturing

The sintering method is pressureless (i.e. without applied pressure on the samples). HighT-Tech had demonstrated continuous roll-to-roll UHS manufacturing. Unlike other high-temperature sintering methods, UHS sintering is achieved through a unique decoupling-coupling design. The heater is away from the sample (decoupled, unlike flash sintering that the electrical current run through the sample), which allows rapid sample change, yet the close distance enables highly effective radiative heat transfer (coupled temperature profile).

HighT-Tech Mission
HighT-Tech Inc. is a spinoff company out of Prof. Liangbing Hu’s lab, with a mission of commercializing the UHS heating platform.
The technology has been widely publicized in the research community after its appearance on the cover of Science. UHS can also be readily extended to a broad range of non-oxide high-temperature materials, including metals, carbides, borides, nitrides, and silicides , because of its extremely high temperature.

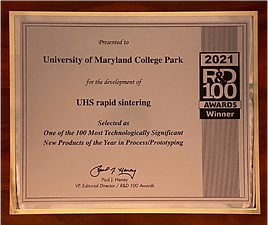